Sustainable Bonding Applications Inside Vehicles – Resource Conservation
Part II
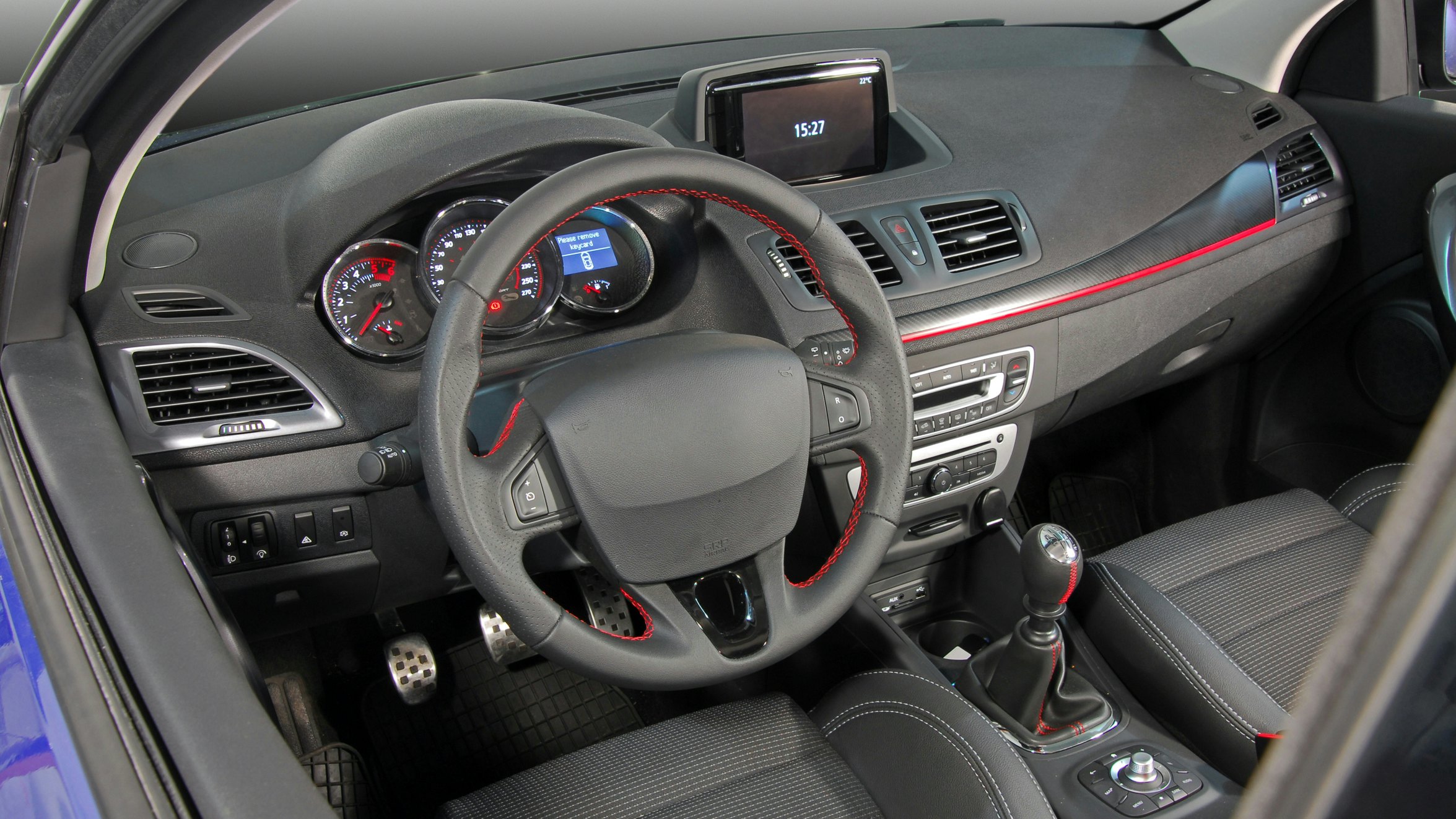
Sustainability is often understood to mean only natural raw materials and recycling. However, environmental responsibility and the conservation of finite resources play a pivotal role in all process stages and are impacted by consumption of energy as well as material. This is also true when it comes to the processing of adhesives. All these aspects are already taken into account when the adhesives are being developed, creating optimized conditions such as lower processing temperatures or reduced total adhesive consumption.
Jowatherm® PUR 613.18 is a PUR hot melt adhesive that saves energy and is gentle on the materials due to its low activation temperature and minimal joining pressure. For example in the lamination process of instrument panels with real leather. Temperature- and pressure-sensitive materials such as leather and spacer fabrics often require a careful balancing act during the lamination procedure. The ideal adhesive has a low application temperature and requires little pressure but provides a bonding resistant to the most demanding climate conditions inside the vehicle.
Jowatherm® PUR 613.18 is quickly tack-free after application and allows an easy positioning of the sewn cover and the spacer fabrics. Once the materials are fixed with seam presses, the adhesive coating is reactivated with hot air. A pressing temperature between 70°C and 80°C of the press platens is sufficient to reach the required re-activation temperature of 55°C to 60°C inside the bondline. After pressing, the laminated instrumented panel can be removed from the warm mold. The initial bonding strength is sufficient—without requiring cooling under pressure. With all the benefits provided by this adhesive, it provides exceptional bonding results. In alternating climate tests, it reliably withstands temperatures over 120°C despite the high stress caused by the shrinking leather.