Succesvolle Verandering
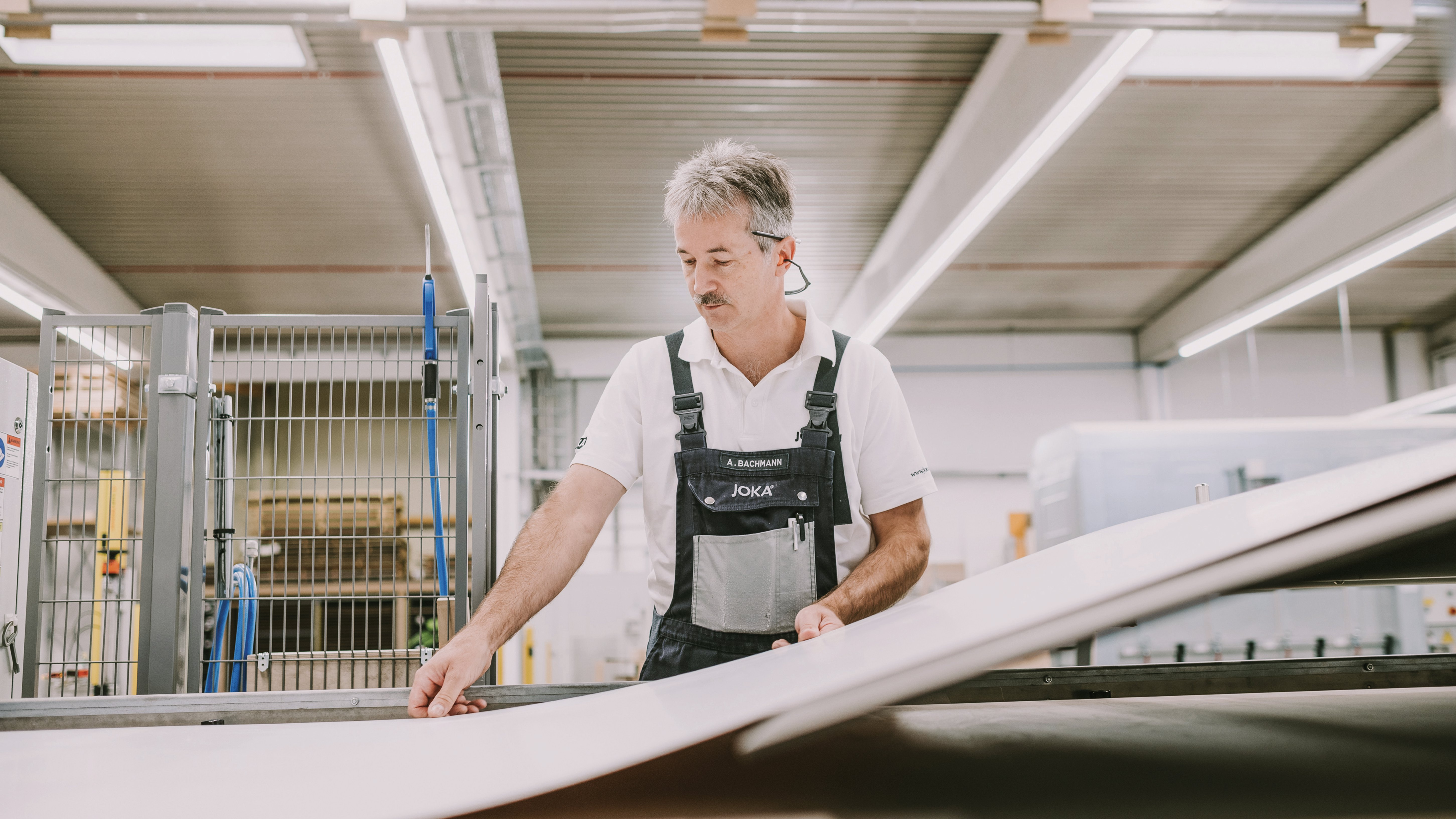
Een middelgroot familiebedrijf uit de stad Kassel, Duitsland, heeft Jordan zich sinds de oprichting in 1919 gepositioneerd als een partner van de handel en ambacht, met een sterke toewijding aan servicekwaliteit en klantgerichtheid. In zijn meer dan 100-jarige bedrijfs geschiedenis is het gegroeid van een niche-aanbieder in de houtsector naar de leidende Europese leverancier van hoogwaardige interieurinrichtingen en goederen, met eigen merken die breed erkend zijn op de markt. De nauwe associatie met de handel was ook de motivatie voor Fred Himmelmann, algemeen directeur bij Jordan in de houtsector, om uit te breiden wat oorspronkelijk een handelsbedrijf was. Daarom werd een interne productieafdeling enkele jaren geleden opgericht. “De vraag naar kant-en-klare meubelonderdelen steeg scherp, samen met een steeds toenemende vraag naar kwaliteit in deze goederen en naar onze flexibiliteit,” reflecteert hij. “Dit is waarom we hebben besloten een interne productieafdeling uitsluitend voor de handel en industrie op te richten.” Fred Himmelmann’s visie: Jordan’s eigen industriële productieafdeling met maximale nabijheid tot de klant en hun behoeften.
“Een partner die denkt zoals wij”
Het zaadje was geplant voor het idee, en de uitvoering van het ambitieuze project volgde snel. Onder leiding van de ervaren meubelmaker Andreas Bachmann werd in 2018 het paneelverwerkingscentrum van Jordan opgericht. Vandaag de dag worden houtgebaseerde panelen in een breed scala aan maten individueel gelamineerd met allerlei materialen in een ultramoderne productieruimte nabij het hoofdkantoor van het bedrijf. Kantenbanden worden op verzoek van de klant aangebracht en de panelen worden via het distributienetwerk van Jordan naar de klant verzonden. Het bestelsysteem is ontworpen om zo flexibel mogelijk voor klanten te zijn. Ze kunnen hun op maat gemaakte panelen 24/7 configureren op het gebruiksvriendelijke online platform en direct bestellen. “We zijn technisch al ingesteld om batchgroottes van slechts één te produceren. En dankzij onze jarenlange ervaring kunnen we onze klanten een selectie van meer dan 800 hoogwaardige HPL-stijlen aanbieden,” legt Andreas Bachmann trots uit. “Maar zonder een partner die denkt zoals wij, zou dit project helemaal niet haalbaar zijn geweest,” voegt hij zichtbaar tevreden toe.
Jowat is ingeschakeld als lijmpartner en heeft geholpen met procesoptimalisatie vanaf de eerste planning van het systeem. Naast hun vergelijkbare bedrijfs geschiedenis en groottes, verbindt vooral één ding de twee bedrijven: werken op gelijkwaardige basis met de klant om zeer servicegerichte en vertrouwensvolle relaties te ontwikkelen. “Industriële laminatieprocessen zijn zeer complex en hangen van veel meer factoren af dan alleen de gebruikte lijm,” legt Thorsten Albers van Jowat Technical Sales uit. “Voorbeelden van andere factoren zijn de initiële kwaliteit van de te lamineren materialen, de lijmapplicatie, de inwerktijden, temperaturen, en luchtvochtigheid tijdens de productie evenals de opslag en transport daarna. Dit heeft een enorme invloed op de kwaliteit en levensduur van het gelamineerde product. De beste situatie voor ons is wanneer we al in de planningsfase bij het project betrokken zijn en samen met onze klant vroegtijdig alle verschillende knoppen kunnen omzetten.”
Van klachten naar nul
De lijmfabrikant zet zich achter de schermen in om de extra mijl te gaan, wat voor Jordan duidelijk waardevol is gebleken. “We kalibreren elk geleverd paneel nogmaals voor de laminering om een optimale afwerking te bereiken. Een automatisch bevochtigingssysteem houdt de omgevingsomstandigheden in de productieruimte altijd perfect. We houden ook lijmlogs bij om de omgevingstemperatuur en luchtvochtigheid voor elke batch te registreren zodat we de best mogelijke kwaliteit kunnen garanderen. De automatische transportsystemen van ons systeem zijn ook ontworpen om de materialen van begin tot eind voorzichtig te behandelen,” legt Andreas Bachmann uit. “Intensieve samenwerking met Jowat heeft ons geholpen om een soepel laminatieproces in het paneelverwerkingscentrum te bereiken. Klachten nemen af naar bijna nul.”
Het lijmproces wordt momenteel onder de loep genomen ter ondersteuning van de arbeidsveiligheid. “Een groot deel van het succes van de paneelverwerkingsoperatie komt natuurlijk van onze medewerkers die daar werken. Bij uitgebreide lijmapplicatie voor vlakke laminatie moeten medewerkers heel dichtbij het proces en de lijm komen. Er is een specifiek risico van di-isocyanaten-bevattende lijmuitstoot die we niet kunnen elimineren,” zegt Bachmann. Met de gezondheid en veiligheid van de medewerkers in gedachten besloot Jordan over te schakelen op niet-gevaarlijke PUR-hotmelt-lijmen en reinigingsproducten voor de gehele paneelproductie.
Tijd- en kostenbesparingen
De PUR-hotmelt-lijmen Jowatherm-Reaktant® MR 609.93 en Jowatherm-Reaktant® MR 608.90 met gevaarloze etikettering worden nu exclusief gebruikt. De verandering van productieprocessen naar de nieuwe monomeerr edu ceerde lijmen voor vlakke laminatie en kantenbanden werd vlekkeloos en zonder kwaliteitsafwijkingen voltooid, dankzij de ondersteuning van de Jowat-experts. “Wat betreft prestaties zijn onze monomeerr edu ceerde producten gelijkwaardig aan conventionele lijmen, zo niet beter. Dat maakt de overstap in de meeste gevallen heel eenvoudig,” legt Thorsten Albers van Jowat uit. “Sommige klanten ervaren zelfs aanzienlijke tijdsbesparingen in het proces wanneer gevaarloze alternatieven worden gebruikt vanwege hun iets hogere initiële sterkte.”
Lijmen met gevaarloze etikettering impliceren ook tijdsbesparingen op een ander vlak. Vanaf augustus 2023 moeten alle medewerkers die werken met di-isocyanaten-bevattende lijmen, zelfs als ze alleen bij de logistiek betrokken zijn, uitgebreide trainingen volgen op regelmatige basis. Dit brengt grote uitgaven van tijd en financiële middelen met zich mee voor bedrijven. “Jowat biedt al bijna 20 jaar monomeerr edu ceerde hotmelt-lijmen aan als alternatief. Onze klanten kunnen deze gebruiken zonder dat ze trainingen hoeven te volgen en bij te houden,” benadrukt Thorsten Albers. “Onze taak is om de klant te adviseren bij de productselectie en hen door een soepele overgang te begeleiden.”
De gevaarloze PUR-hotmelt-lijmen maken deel uit van de Jowat Green Adhesives-lijn en zijn bedoeld om bedrijven te helpen de productieprocessen duurzamer te maken. Naast producten met een focus op arbeidsgezondheid en veiligheid, omvat deze productlijn ook hulpbronnenbesparende en energie-efficiënte oplossingen. De overstap naar lamineren met producten met gevaarloze etikettering is een succes gebleken voor Jordan, wat zeker ook te danken is aan de effectieve samenwerking met Jowat. Een verdere uitbreiding is zeker niet uitgesloten. Met andere woorden, er is potentieel om nog meer gezamenlijk succes te behalen.
Lees andere interessante artikelen in ons klantmagazine.